In our EMEA supply chain survey, we discussed how companies have reordered sourcing priorities, with efforts now aimed at diversifying supply bases and employing near- or onshoring strategies.
Here, we take a deep dive into the implications for the DACH region (Germany, Austria, and Switzerland), revealing the reality check required regarding decreasing dependence on China, plus examples of government incentives in place across a number of sectors.
Our key findings
- Decreasing dependence on China: A strategic imperative, with 84% of respondents across EMEA viewing it as crucial – and even stronger in the DACH region at 88%.
- Plans and progress: Nearly all surveyed companies are actively developing or implementing plans to decrease China sourcing.
- Challenges and solutions: Identifying alternative suppliers and mastering global procurement cost modelling are paramount for DACH companies. India is seen to be the most viable alternative to China, followed by Eastern Europe, Vietnam, Mexico, and Taiwan.
- Government incentives: A pivotal factor in facilitating the transition towards a “China+” strategy.
- Make vs Buy decisions: Critical for future sourcing strategies, yet 20% of DACH respondents lack a concrete plan.
Strategic implications for executives
- The importance of agility in supply chain strategy.
- Investing in global procurement capabilities.
- Leveraging government and local incentives.
Sourcing alternatives is key for DACH companies:
Comparable to other EMEA companies, Make vs Buy strategies and government incentive programs remain important to DACH businesses:
Decreasing dependence on China: A reality check
In the global movement towards de-risking supply chains, the focus on minimizing dependence on China has been particularly pronounced in the United States. However, the European Union, with Germany at its core, reached a critical juncture in this endeavor only recently, in 2022. This shift underlines a broader recognition of the strategic necessity to diversify sourcing away from a single-country dependency that has characterized much of the past decades.
As illustrated above, India is seen as the primary alternative for businesses looking to adjust their sourcing strategies in the future, while countries like Vietnam, Mexico, and the Eastern European region continue to gain traction as viable sources for imports. Nonetheless, these alternatives start from a relatively small base, indicating that the journey towards significant diversification is still in its early stages.
Germany’s reliance on Chinese imports spans a vast array of products. This includes not only consumer goods such as smartphones and clothing but also, more critically, intermediate goods and raw materials essential for various sectors of the German economy. The dependency is starkly evident in the importation of certain electronic and electrical components like batteries and accumulators, along with specific raw materials such as rare earth elements. China’s dominant production capacity and available natural resources in these areas poses a considerable challenge for German industries seeking alternatives.
Moreover, many of the critical raw materials imported from China are indispensable for the production of future technologies, including components vital for electric motors, wind turbines, photovoltaic systems, and other green technologies crucial for Germany’s transition towards a more sustainable economic framework.
Despite the clear understanding within the business community of the need to diversify supply chains and mitigate the dependency on critical imports from China, the path forward is fraught with complexity. The process of finding alternative sources is intricate and anticipated to be prolonged, especially for goods where China holds a leading global production role or where alternatives are scarce. This situation underscores the necessity for a strategic and methodical approach to reduce dependency on Chinese imports, balancing immediate economic needs with long-term sustainability and resilience objectives.
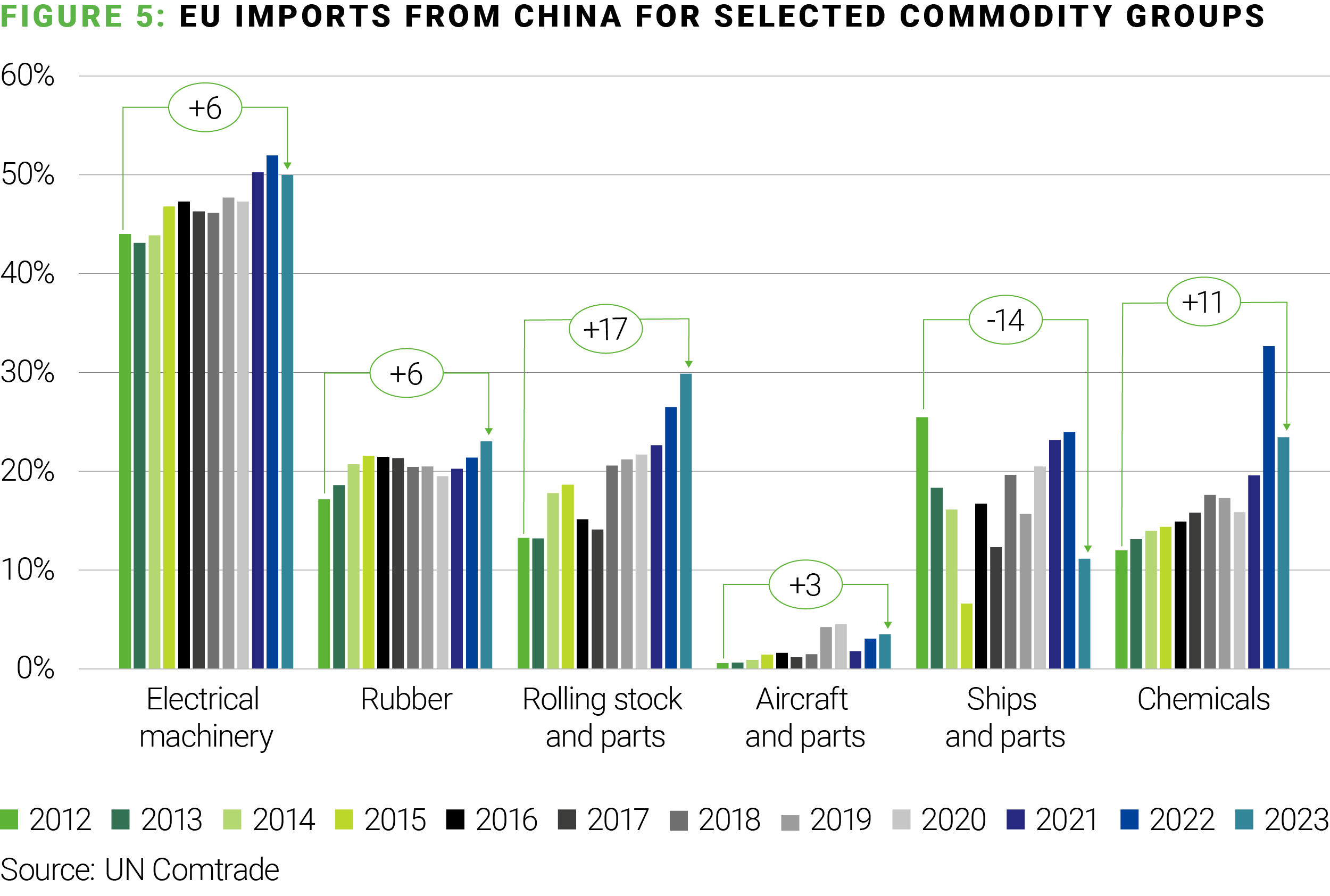
As reflected in the earlier table above, the importance of government incentives cannot be understated, with two sectors in particular drawing significant attention in this respect:
Government incentives: Semiconductor sector
The German Government is actively deploying financial incentives to entice semiconductor companies to establish production facilities within the country. This strategic move, particularly in the semiconductor industry, is bolstered by Germany’s desire to become a pivotal node in the global semiconductor supply chain. Given the sector’s minimal labor intensity, the disadvantage of higher labor costs in Germany is offset by the availability of highly skilled labor and the attractive incentives on offer.
Notable investments in this sector include:
- Intel in Magdeburg: A substantial investment of €30 billion is earmarked for a new facility, with a €10 billion subsidy proposed. The planned start of production is in 2024, with the facility expected to be operational by 2029.
- TSMC in Dresden: Traditionally focused on its Taiwanese production, the Taiwan Semiconductor Manufacturing Company (TSMC) is branching out to Dresden with a €5 billion subsidy to mitigate risks associated with political tensions with China. This diversification effort will see TSMC operating in conjunction with Infineon, Bosch, and NXP, with production slated to begin this year.
- Infineon in Dresden: Infineon is set to expand its existing plant with a €5 billion investment, seeking a €1 billion subsidy. The expansion started production in 2023 and open by 2026.
- Wolfspeed in Saarland: Planning a €3 billion investment for a new facility, Wolfspeed aims for a subsidy of approximately €600 million, with production starting in 2025 and the opening scheduled for 2026.
All the aforementioned subsidies are pending approval from the European Union. The projects are likely to be supported by the Klimatransformationsfonds (“Climate Transformation Fund”), the “EU Chips Act”, and/or IPCEI (Important Projects of Common European Interest).
Government incentives: Steel sector
The steel industry in Germany is another beneficiary of government subsidies, particularly aimed at addressing the challenges of emissions reduction. The transition to emission-free steel production is supported through significant financial incentives:
- Thyssenkrupp in Duisburg: A €2 billion subsidy has been granted for upgrading the plant to produce green steel. This funding is part of a larger investment requirement, with additional funding at risk due to legal challenges against the Klimatransformationsfonds. The project, approved by the EU in July 2023, started production in 2023 and open in 2026.
- ArcelorMittal in Bremen and Eisenhüttenstadt: Targeting decarbonization projects, ArcelorMittal is poised to receive €1.3 billion, with operations expected to commence in 2026. The subsidy was approved by the EU in February 2024.
- Salzgitter Flachstahl: Secured a €1 billion subsidy for its decarbonization efforts, with the subsidy approved by the EU in April 2023. The project began production in 2023 and become operational by 2026.
- Funding for these initiatives may also come through “IPCEI Wasserstoff” (Important Projects of Common European Interest – Hydrogen), underscoring the strategic emphasis to transform the steel industry into a greener and more sustainable sector.
These concerted efforts in both the semiconductor and steel sectors highlight Germany’s strategic positioning and commitment to not only diversify its supply chains but also to embrace and lead in the transition towards a more sustainable and technologically advanced industrial landscape.
Government incentives – Battery technology
Europe’s ambition to bolster its technological sovereignty is vividly illustrated by its recent initiatives to localize battery technology and manufacturing. With an eye on electrification and sustainable energy solutions, significant investments, strategic acquisitions, and targeted policy incentives are paving the way for a resilient battery manufacturing ecosystem across the continent.
The landscape for lithium-ion battery (LIB) manufacturing in Europe is evolving, driven by the need for local value creation and European sovereignty over LIBs. Initiatives like the European Battery Alliance, and research programs “Horizon 2020” and “Battery 2030+”, exemplify the concerted efforts to anchor manufacturing within Europe:
- CATL
- Group14 Technologies’ acquisition of Schmid Silicon Technology Holding GmbH, which marked a significant leap towards bolstering the global battery supply chain with advanced silicon battery technology. This strategic move, enhancing Schmid Silicon’s silane factory in Spreetal, Germany, aligns with the EU’s decarbonization goals and emphasizes Europe’s dedication to advancing high-energy density battery materials.
- Tesla in Berlin
- Northvolt in northern Germany
These are supported by significant investments aimed at fostering LIB ventures and constructing mega-factories, despite the challenges and competition from dominant Asian manufacturers. In addition, the competitive landscape faces threats from attractive investment conditions in the US. This situation points to the need for EU-wide support and streamlined approvals to bolster continental battery production. Through strategic acquisitions and policy incentives, Europe is actively shaping its energy transition narrative, emphasizing local manufacturing, sustainability, and innovation.
Recommendations
The path forward: Building resilient, cost-efficient, and diversified supply chains.
- Strategic imperative of diversification: With an overwhelming majority recognizing the need to reduce dependency on China, diversification is no longer optional but a strategic necessity for resilience and competitive advantage.
- Challenges Ahead: The transition entails significant challenges, notably finding capable alternative suppliers and understanding the cost implications of diversification. However, these are surmountable with the right strategies and investments, particularly in global procurement cost modelling.
- Leveraging incentives: Executives must navigate and leverage government and local incentives effectively to facilitate the transition, with a notable disparity in readiness between EU and US incentives.
- Strategic decision-making: The Make vs Buy decision is crucial in this transition, requiring a strategic approach to evaluate and implement sourcing options that align with corporate goals and market dynamics.
- Future-proofing through agility: Building a supply chain that is not only resilient but also agile and cost-efficient is paramount. This includes exploring nearshoring opportunities and investing in capabilities that enhance supply chain visibility and flexibility.
This approach offers a comprehensive view for executives, emphasizing the need for strategic planning, agility, and leveraging incentives to navigate the shift away from China-dependent supply chains, towards a more diversified and resilient model.