In the race to net zero it is easy to become mired in what can be controlled, where the greatest impact can be made, and how it can be measured. It’s particularly true for automotive OEMs when looking at Scope 3 emissions, covering a wide range of activity from waste disposal to an expansive supply chain.
Globally, a typical OEM's Scope 3 emissions account for, on average, 95% of all emissions – and that’s after excluding the hugely variable impact of vehicle use (see our previous blog on Scope 3 emissions for further details).
The largest percentage of these emissions is the 68% accounted for by “Purchased Goods and Services” – all the ‘car parts’ that go into a vehicle.
While there are a number of routes to follow to cut emissions in the 15 categories that make up Scope 3, it’s an area complicated by questions over impact, supplier relationships, and data management.
It can be hard to know where to start. However, interrogating how materials are processed can present a clear direction towards emissions reduction action – and some quick wins.
Finding focus on Scope 3
A strategy many car producers have explored to cut vehicle emissions is light-weighting – for example, by replacing some steel content in a car for lighter-weight aluminium. This can have a dramatic impact on vehicle weight (and consequently impacts tailpipe emissions), but can actually drive up production emissions:
- 1.9kg CO2 equivalent (CO2e) emissions emitted per 1.0kg of Steel (global average)
- 16.1kg of CO2e emitted per 1.0kg of Aluminium (global average)
That is, aluminium generates, on average, almost three times the emissions of steel (considering that aluminium is approximately one third the weight of steel). This is largely due to the fact that global metal production still largely relies on non-renewable or black energy, such as coal.
Let’s take a specific example: a car with Purchased Goods & Services (i.e., vehicle parts) contributing, say, 10,000kg of CO2e and 200kg aluminium content (these figures are not atypical of an average vehicle today). Let’s also assume this car is manufactured using a mix of black, green and recycled material – i.e., the emissions generated tie up with the global averages mentioned above.
We want to light-weight our car by increasing the aluminium content by 50% (replacing steel content). If we don’t change the energy source, light-weighting the vehicle actually exacerbates Scope 3 emissions – increasing our “Purchased Goods and Services” category by more than 2%.
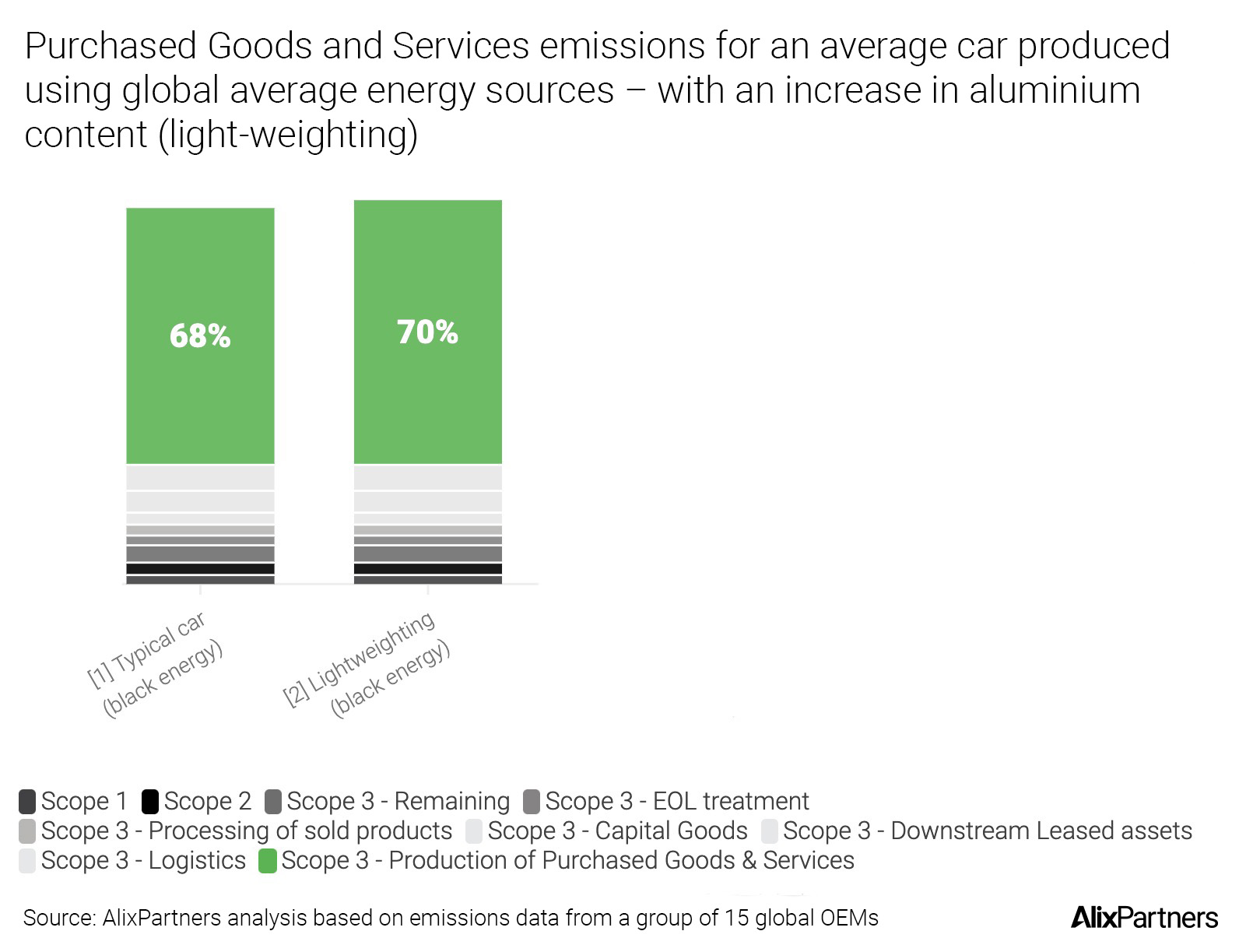
So, while this example of ‘light-weighting’ (replacing steel for aluminium) could reduce tailpipe emissions by around 12 grams CO2/km, our car would need to drive over 80,000km before the emissions savings from having a lighter vehicle offset the higher production emissions generated in increasing the aluminium content of the vehicle.
There are two key approaches OEMs could use to tackle production emissions at supplier source through vehicle materials, rather than attempting to realise emissions savings during vehicle use:
- Using green energy throughout the supply chain
- Sourcing components with a higher content of recycled materials
Reduce Scope 3 Emissions with green energy
While light-weighting with aluminium (without changing the energy source) increases Scope 3 emissions and takes over 80,000 km to ‘breakeven’ from the tail-pipe effect, sourcing aluminium produced using green energy has a positive impact on these emissions.
Green energy can cut emissions associated with these metals by approximately 80%. In our comparison with the increased aluminium content, Purchased Goods and Services emissions fall from 70% to 57%.
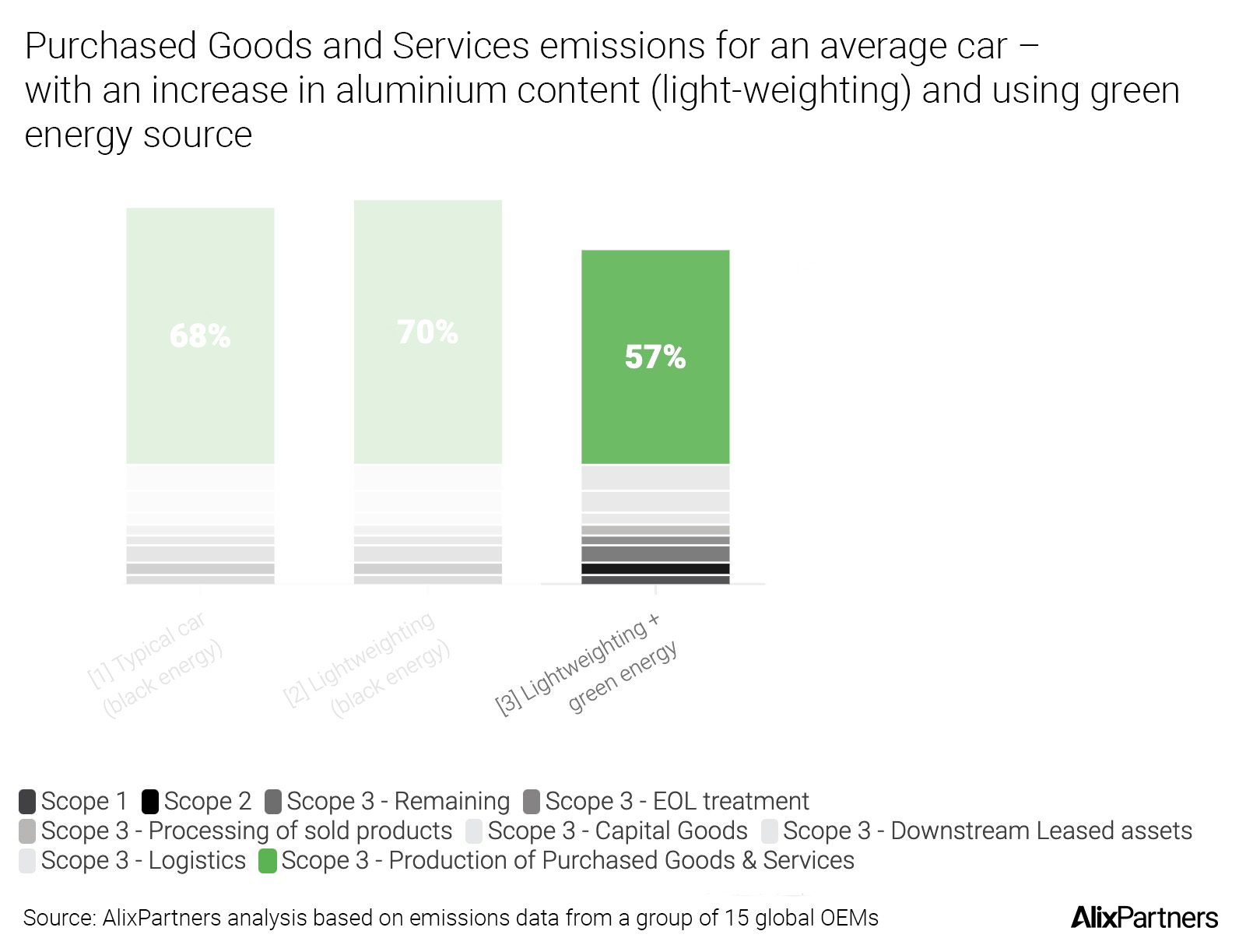
Whether this can be done in practice will often depend on supplier locations and supplier initiatives. A supplier in Sweden, for example, will find it easier to source renewable energy as 60% of Sweden’s energy supply comes from renewables (with a substantial proportion of the remaining energy coming from nuclear power). Conversely, a supplier in Poland will have to demonstrate high levels of initiative – and possibly require greater investment – to source renewable energy, as only 16% of the country’s energy mix is renewable (with nuclear power planned to go online from early next decade).
Reduce Scope 3 emissions with recycling
Metals have a great capacity for recycling while maintaining structural integrity and significantly lowering the energy required. Steel can be infinitely recycled with approximately 60% lower energy needed to create the finished product. Recycled aluminium can also maintain integrity with minimal material loss (around 1-2%) and a huge energy reduction (up to 95%) compared with producing primary (new) material.
In our light-weighting example scenario above, combining green energy sourcing with recycled metal content for both aluminium and steel creates a further reduction of Purchased Goods and Services emissions, down to 52%.
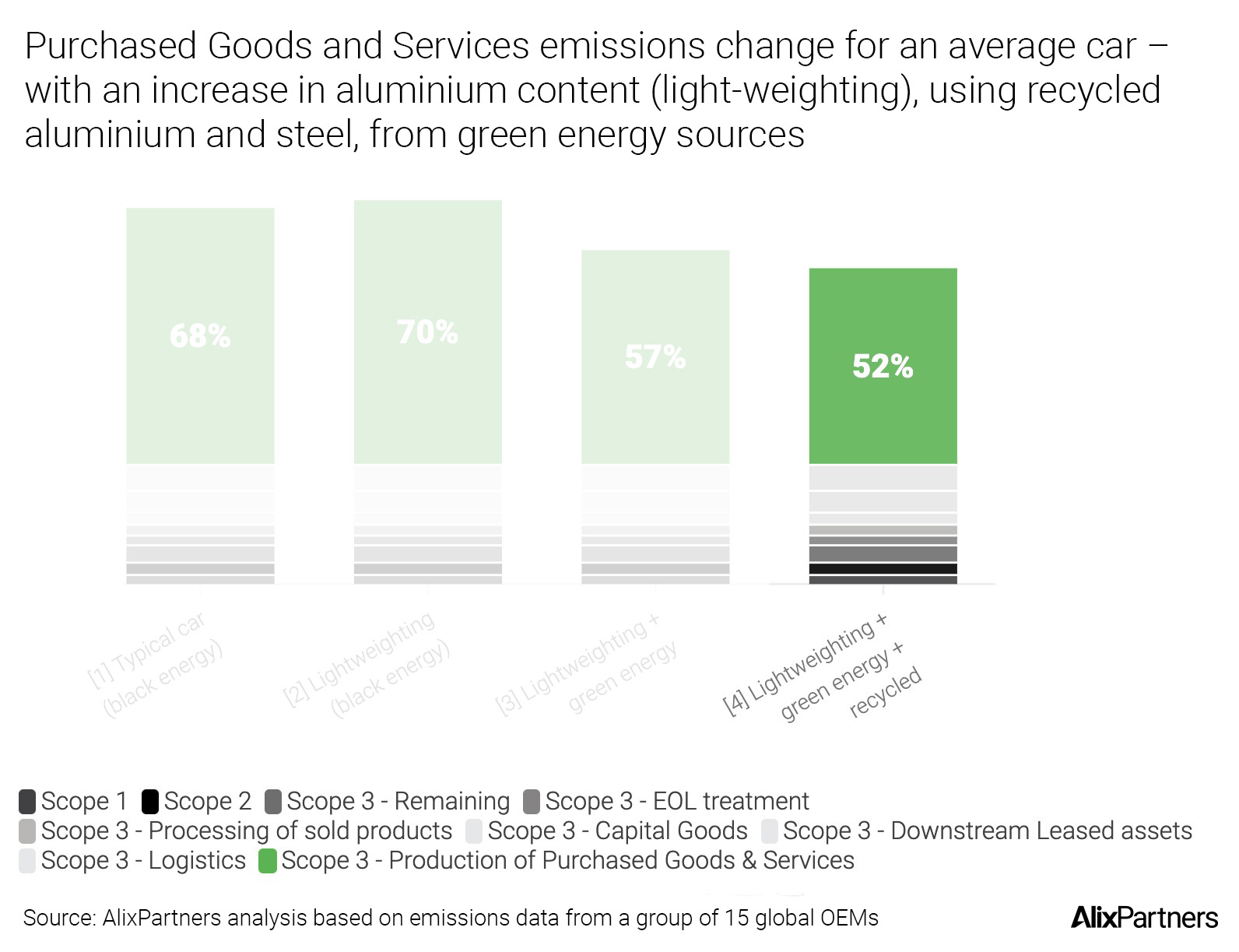
What if we forego the light-weighting and source purely recycled steel and aluminium produced using green energy? Although the tailpipe emission benefit won’t be realised, we find the overall emissions associated with the vehicle product itself is almost the same as the light-weighting – reducing emissions from the original 68% down to just 52%.
A scope 3 strategy for OEMs
In the complex area of OEM Scope 3 emissions, it can be hard to know how to interrogate the emissions information from suppliers, and the trust you can apply to data when considering the information links through Tier 1 suppliers to suppliers further down the chain – all the way down to raw material mining.
If not actioned already, OEMs should update their standard QCD supplier performance metrics to QCDE (Quality, Cost, Delivery and Emissions) – if not the more encompassing Environmental, Social, and Governance. Increasingly, suppliers – particularly those ‘going green’ – are actively promoting how they process materials and the associated CO2e impact. By expanding required performance metrics to include emissions in sourcing vehicle components and systems with potential suppliers, it is possible to lower the emissions of the components – and often for a lower cost than if those components were made with virgin metals.
Tackling energy-intensive metal production is just one example of how more extensive research into production methods reveals the true emissions-cutting potential. Finding these focus areas to interrogate and act on, whether in Purchased Goods and Services or other major Scope 3 category such as Transportation and Distribution, is key for OEMs to make secure and sustainable gains towards net zero.